Wet-Dry Vibratory Passivation of Heat-Treated Parts in One Machine
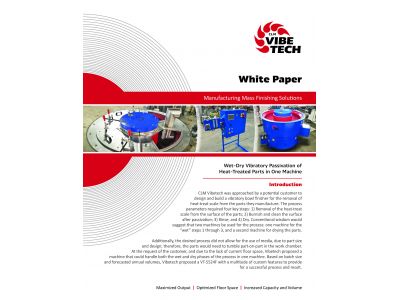
Tags: Customization, Mass Finishing, Solutions, Vibe Equipment, Vibetech, Vibratory Machines
Wet-Dry Vibratory Passivation of Heat-Treated Parts in One Machine
Introduction
CLM Vibetech was approached by a potential customer to design and build a vibratory bowl finisher for the removal of heat-treat scale from the parts they manufacture. The process parameters required four key steps: 1) Removal of the heat-treat scale from the surface of the parts; 2) Burnish and clean the surface after passivation; 3) Rinse; and 4) Dry. Conventional wisdom would suggest that two machines be used for the process: one machine for the “wet” steps 1 through 3, and a second machine for drying the parts. Additionally, the desired process did not allow for the use of media, due to part size and design; therefore, the parts would need to tumble part-on-part in the work chamber. At the request of the customer, and due to the lack of current floor space, Vibetech proposed a machine that could handle both the wet and dry phases of the process in one machine. Based on batch size and forecasted annual volumes, Vibetech proposed a VT-5524F with a multitude of custom features to provide for a successful process and result.
Machine Design
For the process to work in a single machine, the machine design and function needed to be able to meet the following demands:
- The process would not allow for the use of media, so the machine needed to be able to handle part-on-part tumbling. A 95-durometer polyurethane liner was chosen for this application, to provide a longer service life of the liner.
- Because media could not be used in the washing or drying process, the parts would need to be dried with heated air. This required the process channel of the machine to be enclosed with a rigid stainless-steel lid to effectively deliver and trap the heated air.
- To make the drying process efficient, a drain-line vacuum was used to quickly remove excess water from the process channel prior to and during the drying phase.
- Dual compound metering pumps were used to deliver the passivation and cleaning/burnishing chemistries.
- To load the parts into the process channel, the lid required a hinged loading port. In addition, the customer requested sealed viewing ports to visually inspect the work chamber during the process.
- Electric heat was desired, and the heater/blower system needed to be remotely located and mounted to the wall behind the machine, to save floor space. High temperature duct-hose was used to deliver the heated air. A 12KW duct heater was used with a 1200 CFM blower at 4” SP to provide the heated process air.
- To allow the parts to exit the process channel, Vibetech used our pneumatic unload plunger, which is located at the bottom of the process channel of the bowl, providing for a quick and efficient unloading of the parts.
- The machine and process needed to be controlled by a PLC and HMI interface on the control panel.
- After loading, sequencing of the multi-step process needed to be fully automated.
Conclusion and Results
The machine was put into service in the summer of 2005. The customer was pleased with the quality and durability of the machine, along with the continued customer service that Vibetech has provided throughout the years. In 2019, the demand for their product increased, and they purchased an additional machine to keep up with production. Shortly after, the Covid pandemic occurred, which provided for an even greater demand and opportunity for the product that they manufacture. Vibetech was approached for three more additional units and was asked to produce the machines as quickly as possible so that the customer could take advantage of this increased demand for their product.
The management team at Vibetech met and developed a manufacturing plan to decrease the lead time on the three units by as much as 40%, at no additional charge to the customer. The machines were built and delivered on time, allowing the customer to meet the ever-increasing demand from their end users. By accomplishing this wet-dry finishing process in one machine, output was maximized with less floor space required, allowing for the purchase of additional capacity through equipment.
“CLM Vibetech, Inc. takes pride in working with its distributors and customers to help provide mass finishing solutions along with THE BEST CUSTOMER SERVICE in the mass finishing industry.”
- Matt Harma, CFO/Owner, CLM Vibetech, Inc.