Media-Free Finishing System Designed for Ammo Companies Solves Challenges for Other Industries
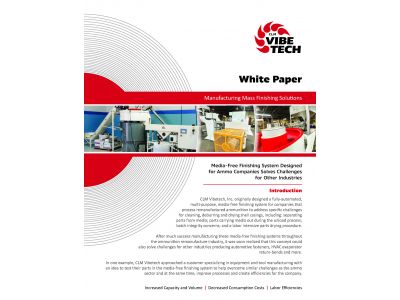
Tags: MassFinishing, Media-Free System, Solutions, Vibetech
Media-Free Finishing System Designed for Ammo Companies Solves Challenges for Other Industries
Introduction
CLM Vibetech, Inc. originally designed a fully-automated, multi-purpose, media-free finishing system for companies that process remanufactured ammunition to address specific challenges for cleaning, deburring and drying shell casings, including: separating parts from media; parts carrying media out during the unload process; batch integrity concerns; and a labor intensive parts drying procedure.
After much success manufacturing these media-free finishing systems throughout the ammunition remanufacture industry, it was soon realized that this concept could also solve challenges for other industries producing automotive fasteners, HVAC evaporator return-bends and more.
In one example, CLM Vibetech approached a customer specializing in equipment and tool manufacturing with an idea to test their parts in the media-free finishing system to help overcome similar challenges as the ammo sector and at the same time, improve processes and create efficiencies for the company.
How the System Operates
The system consists of a 1.5 to 20 cubic foot capacity vibratory bowl finisher, a vibratory hopper/feeder, and rotary drum dryer. Parts are loaded into the vibratory bowl finisher, where they are tumbled part-on-part. During this phase, the tumbling action of the parts impinge and burnish themselves, eliminating the need for expensive steel media. While processing, cleaning compounds and water are sprayed onto the tumbling mass, cleaning the parts internally and externally.
Once the desired cleanliness is achieved, the vibratory bowl shuts down for a pre-determined amount of time to drain off excess solution in the process channel. At this time, the unload-plunger (a unique, unload plug located in the bottom of the process channel and found only on Vibetech machines), is powered to the unload position by a pneumatic cylinder. This allows the cleaned parts to exit the vibratory bowl quickly and effectively, into the hopper of the vibratory feeder, which also provides batch integrity (ensuring all parts actually leave the machine). The bowl turns back on, vibrating the mass around to the opening of the plunger quickly. The resulting unloading of the parts is quick, efficient and hands-free.
Once the unload is complete, the plunger is actuated back to a closed position, allowing for the processing of the next batch of parts, while the drying process takes place. The parts are then fed into the rotary-drum dryer by the vibratory hopper feeder, eliminating the inefficiencies of transporting parts to another area of the facility for drying. The vibratory hopper feeder utilizes an electromagnetic drive that powers the feeding of the parts into the dryer. The feed rate of the dryer is controlled by a variable frequency drive.
Once in the rotary drum dryer, the parts are pulled through the drum with an integral set of flights as the drum rotates. As they travel through the drum, the parts also pass over tumble strips, which lift the parts and invert them during drum rotation, providing for better water drainage from the internal areas of the parts. The entire time parts are travelling through the dryer, recirculated heated air is forced through the drum, reaching temperatures as high as 250° F, drying the parts inside and out. Parts are unloaded automatically into approved containers once leaving the drum. The entire system is fully automated and controlled from a simple to use touch screen on the main control panel.
Key Results
In the example noted above, CLM Vibetech was able to successfully test parts in the media-free system for the customer by eliminating media from being carried into downstream equipment; achieving the company’s desired finishing result by cleaning the outside of their parts, as well as cosmetically correcting the mouth edges of the parts effectively; eliminating the process of separating parts from media; providing a smaller, less expensive machine, freeing-up valuable floor space; and improving their drying process.
By eliminating the need for costly finishing media, the process is simplified, and run capacity increases per batch, which inflates daily output. Additionally, consumption costs decrease and there is no longer a need to account for, or be concerned about, media level losses created by parts carrying media out during unload or lodging in areas within the parts themselves. Furthermore, the unique pneumatic unload plunger ensures parts leave the machine, eliminating part contamination concerns.
In conclusion, by incorporating the CLM Vibetech fully automated, media-free finishing system, challenges in numerous industries are eliminated regarding media loss, batch integrity and inefficient separate processes for cleaning, deburring and drying. Additionally, companies experience increased capacity and volume, labor efficiencies and decreased consumption costs, which makes future growth more attainable.
“CLM Vibetech is pleased to assist our customers in solving problems and streamlining processes. Our media-free finishing system for parts cleaning, deburring and drying is essentially three engineered machines that work together effectively, providing full automation for cost effectiveness; a unique pneumatic unload plunger for batch integrity; and an easy-to-use touch screen control panel for labor efficiencies.”
- Bill Money, President, CLM Vibetech, Inc.