How a Bijur Auto-Oil-Recirculating System Works and How to Maintain It -- Part 2
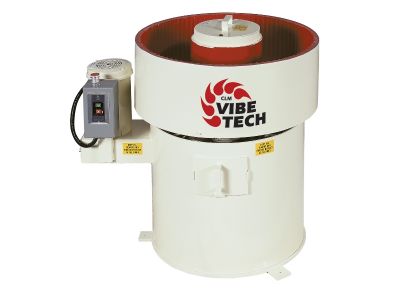
Tags: Vibratory Finisher
The pump draws oil from the reservoir, through a suction filter, which strains large debris from the pump. This flow of oil is then pumped through an external filter assembly, consisting of an aluminum housing, sintered filter element, and o-rings. The bottom of the filter housing spins off, making changing or cleaning the filter quick and easy. The filter element is a 25 micron sintered cup, in which the oil diffuses through the element wall, trapping debris and contaminants, before exiting the housing. Once the oil has pumped through the filter assembly, it then passes through an oil flow-sensor. As the oil flows through the sensor, a small brass piston is raised by the oil flow, compressing a small spring. When oil-flow is sufficient, the piston, which has a small magnet at the head of it, closes a sensitive contact, which sends a signal back to the panel that adequate oil-flow is detected. If oil-flow decreases for any reason, such as a dirty filter or ruptured lube line from the filter to the flow-sensor, the spring pushes the piston back down away from the contact, and the circuit is broken. This shuts power off at the main control panel. Since the lubricator puts out 120cc’s of oil per minute, the flow sensor is calibrated to cut power to the machine if oil flow drops below just under 50%. This type of flow sensor that is being used has proven very reliable in providing oil-flow detection. From the flow-sensor, the oil is carried up to the top of the drive-cartridge (this is the removeable bearing-housing, drive-shaft assembly), located in the center of the bowl. The oil in-feed line delivers the oil to the bearing retainer end cap. The oil lubricates the top bearing, and passes through the internal cavity of the drive-cartridge, lubricating the bottom bearing as well. From there, the oil is gravity fed from the bottom bearing end cap, back to the lube unit. At this point, the oil remains in the reservoir, where it has time to dissipate some of the heat created from machine operation, before it is recirculated. This design allows for continuous lubrication of the bearings, filtering of the oil, and heat dissipation from operation.
To prolong bearing life and performance of the machine, here is a checklist of preventative-maintenance items.
- Change oil and filter (element located in filter housing) every 1000 machine run hours
- At each oil change, remove the reservoir from the pump, and drain off oil and clean thoroughly. Simply wipe inside of reservoir with a clean, lint-free rag or paper towel.
- Use either MOBILGEAR 600 XP 68 (conventional) or MOBIL SHC 626(synthetic). For use with ALL Vibetech equipment set up for Auto-Oil-Recirculating systems.
- Clean the suction screen filter located on the bottom of the pump assembly with every oil change. Filter unscrews from the plumbing. Soak in a light solvent (mineral spirits) for several minutes, and blow clean with compressed air.
- Flow sensor should be disassembled for cleaning with each oil change. Remove lube lines and flow sensor from mounting bracket. To disassemble, unthread the lube-input block from the bottom of the flow sensor. The flow sensor piston/cup and spring can now be removed. DO NOT CLEAN IN SOLVENTS. Simply wipe clean with a lint-free rag, or paper towel. Blow the inside of the sensor out with compressed air. Re-install the spring, and then the piston/cup. Now thread the lube input block back onto the sensor. Make sure to only tighten hand-tight. DO NOT USE TOOLS TO TIGHTEN THE LUBE INPUT BLOCK BACK ONTO THE SENSOR. Over-tightening with tools may damage the sensor.
- If service is being performed following a bearing failure, there is a chance for considerable bearing/cage material building up in the lube unit. Clean as described above. In addition to this, remove all lube lines that either deliver oil to the drive-cartridge assembly, or return oil back to the lubricator. Flush these lines out with a mild solvent (mineral spirits) and blow compressed air through the lines to aid in removing any bearing debris that could have built up after the bearing failure.
- Lubricator outputs 120cc’s of oil/minute. It is good practice to check this monthly. Simply disconnect the lube line from the output of the flow sensor to the coupling welded into the base wall. Hold this line over a clean container, and turn the pump on at the control panel. Collect the oil in the container for 1 minute. Measure the oil collected. If the amount of oil collected is less than 3 ounces, check filter in filter assembly. Replace as needed. Although the flow sensor is monitoring oil flow during operation, it will not shut the machine down as filters slowly become dirty. Flow sensors are more of a safe-guard against catastrophic losses of oil flow, such as ruptured lube lines or a blown fuse on the lube pump, which result in sudden loss of oil flow.
- Filter Elements can be cleaned one time only, and preferably only when a replacement filter is not available. To clean the element, soak in mineral spirits (Do Not Use Any Other Type of Solvent). Soak for 5-10 minutes. Remove element, and encase if a lint-free rag or paper towel. Apply compressed air from inside the cup, forcing air-flow through the wall. Trapped debris and contaminants will collect of the rag or towel. Continue until cleaned. Re-install into the filter housing.
- Always try to cut down on the incidence of water coming in contact with the lubricator. Evidence of eater in the lube system is a greyish/brown muddy look to the oil. Trace the source of contact, and eliminate the exposure.